CASE STUDY
RapidWeld
OVERVIEW
Client info
RapidWeld is a collaborative project involving SSE Renewables, Cambridge Vacuum Engineering (CVE), DNV, Sif Netherlands B.V, Agile NDT and The Welding Institute (TWI). The companies joined forces to explore the benefits of electron beam (EB) welding in the creation of wind turbine monopiles.
Using funding from Innovate UK, the RapidWeld team wanted to demonstrate that electron beam (EB) welding is significantly quicker, cheaper, cleaner and more energy efficient than existing techniques. The team also wanted to try to produce higher quality welds with excellent fatigue properties.
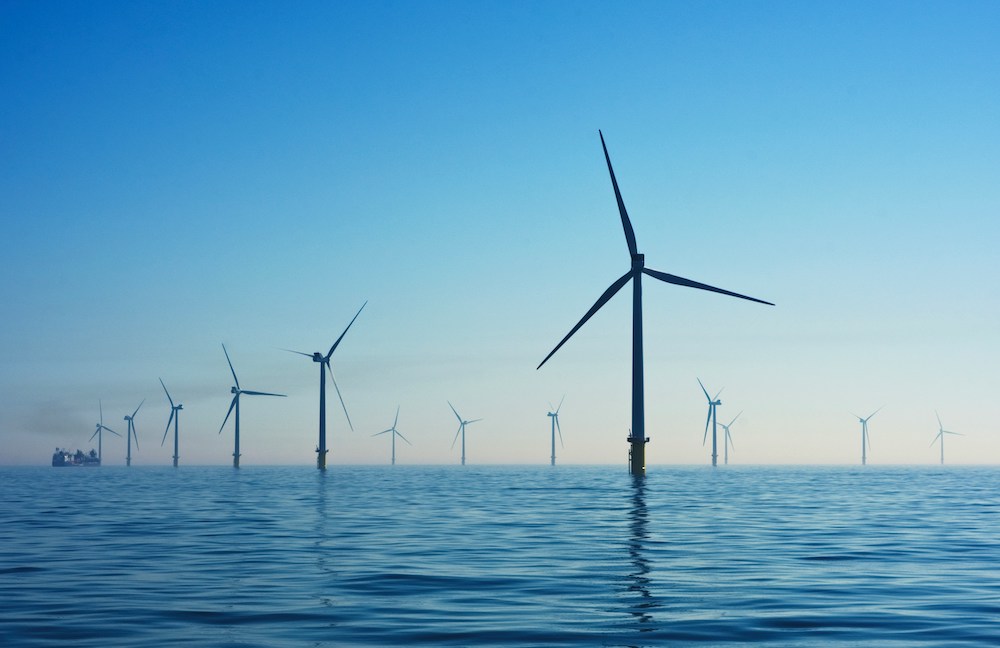
The problem
The development of wind turbines for offshore locations like the North Sea presents many technical and logistical challenges. Creating turbines and foundation pieces that can withstand extreme marine conditions requires welds of the highest quality and consistency.
This can involve lengthy production timescales that are out of kilter with the sustainability goals of energy companies and the race to net zero. Currently, wind turbine monopiles – a critical component of wind turbine foundations – are typically fabricated using traditional welding methods such as submerged arc welding (SAW). However, these methods are limited in terms of speed, cost, and the quality of welds produced.
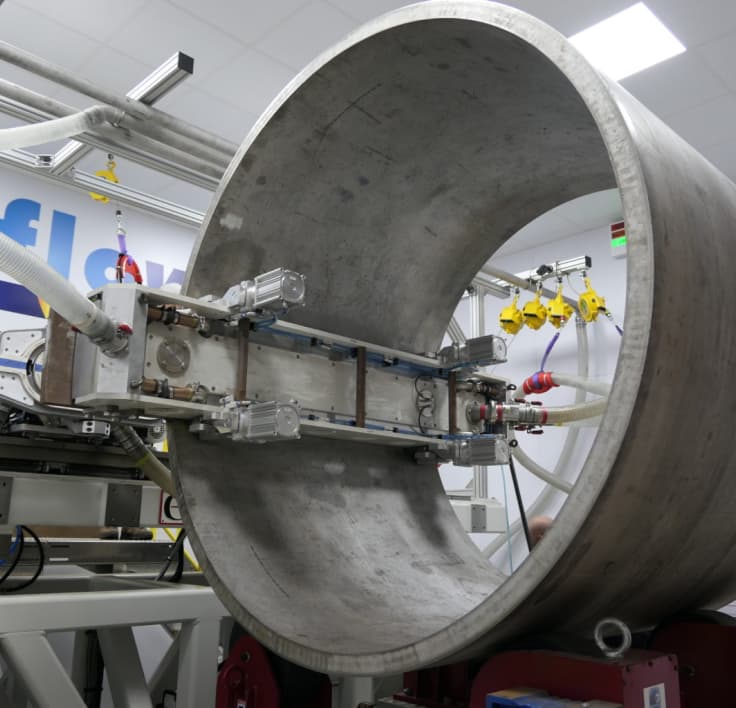
The solution
Working together, using Ebflow, the RapidWeld team set about creating a monopile foundation for the Dogger Bank Wind Farm project. An Ebflow machine was installed at Sif’s Maasvlakte 2 facility in Rotterdam.
The machine was to perform several longitudinal welds on 2750 mm length seams on 8m diameter rolled cans with a wall thickness of between 69-85mm.
The plan was for resulting samples to be assessed in accordance with DNV-OS-C401, the standard for ‘Fabrication and Testing of Offshore Structures. Concurrently, Dogger Bank also planned to commission fatigue testing to ensure the welds could deliver over 20 years of offshore service.
The results
Using Ebflow the Rapidweld team welded the first-ever electron beam welded foundation piece for the Dogger Bank turbine monopile – with dramatic results. The piece was welded at least 25 times faster than the current default manufacturing method. Production required 90% less energy and cost 88% less. The approach also produced 97% less CO2 emissions.
Crucially, the quality of the weld met the mechanical and metallurgical properties needed to satisfy construction codes and design requirements.
The resulting monopile has subsequently been shipped to and installed at the Dogger Bank Wind Farm, where it is helping to generate clean, green energy.
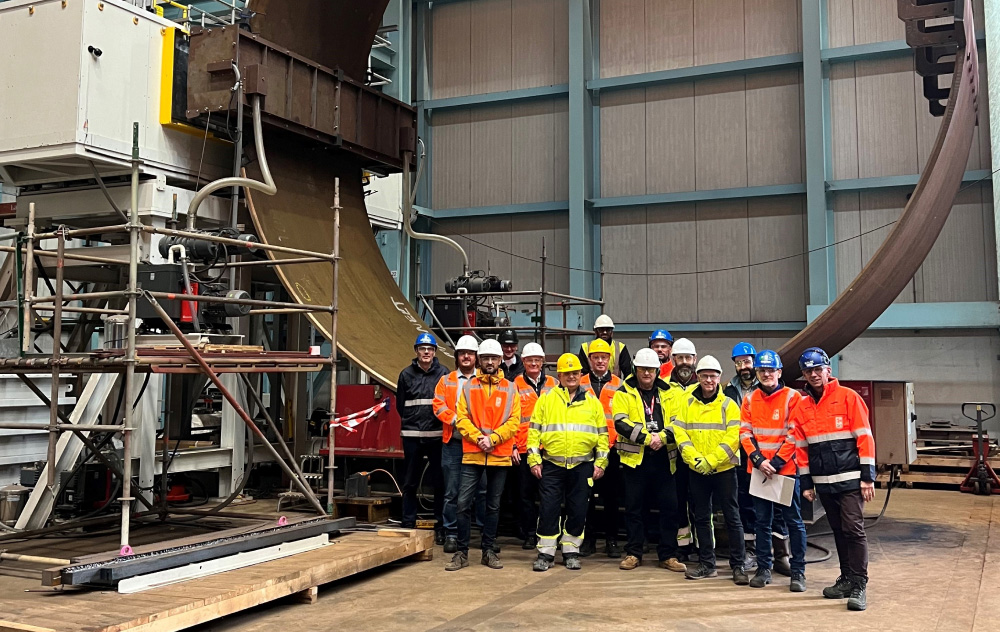
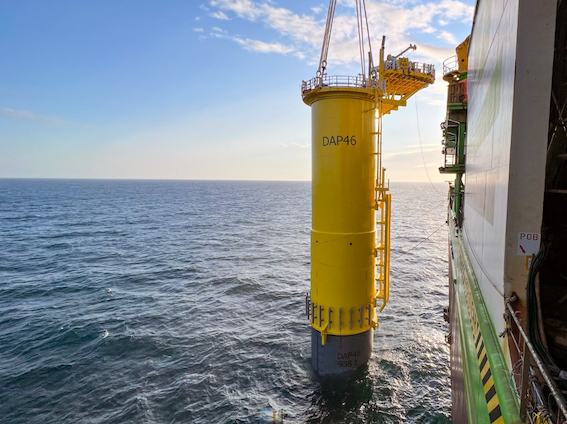
What next?
The validation of Ebflow for offshore projects has huge implications for the energy sector’s net zero ambitions. The significant time and cost savings achievable with Ebflow have the potential to help accelerate the delivery of more wind farms worldwide.
Ebflow also requires less energy and does not require the use of consumable materials like fillers. This makes it possible to reduce the carbon footprint associated with the manufacture of core green energy infrastructure components.
Furthermore, because Ebflow is easily transportable, the technology can unlock additional carbon emission savings by increasing opportunities for the local manufacture of infrastructure components close to customers or engineering project locations.
In the case of wind turbines, this could prove particularly beneficial in Europe. Currently, many wind farm monopiles, jackets and towers are sourced from the Far East, which involves shipping large components incredibly long distances.
What our customers say
This is a ‘first-in-class’ project, establishing this UK innovation as a world-leading technology. With monopile type foundations accounting for over 90% of foundations used in UK projects, Ebflow RPEB could realise significant cost savings on future projects. These substantial savings will not only benefit the UK offshore engineering industry but could be passed on to UK energy consumers.
Olly Cass
SSE Renewables Project Director for Dogger Bank Wind Farm