SECTORS
Breaking boundaries
Ebflow is a highly versatile electron beam power welding system that can be used in a variety of applications, across a wide range of industries.
From oil and gas to nuclear power generation to shipbuilding and more, Ebflow is changing the world of welding.
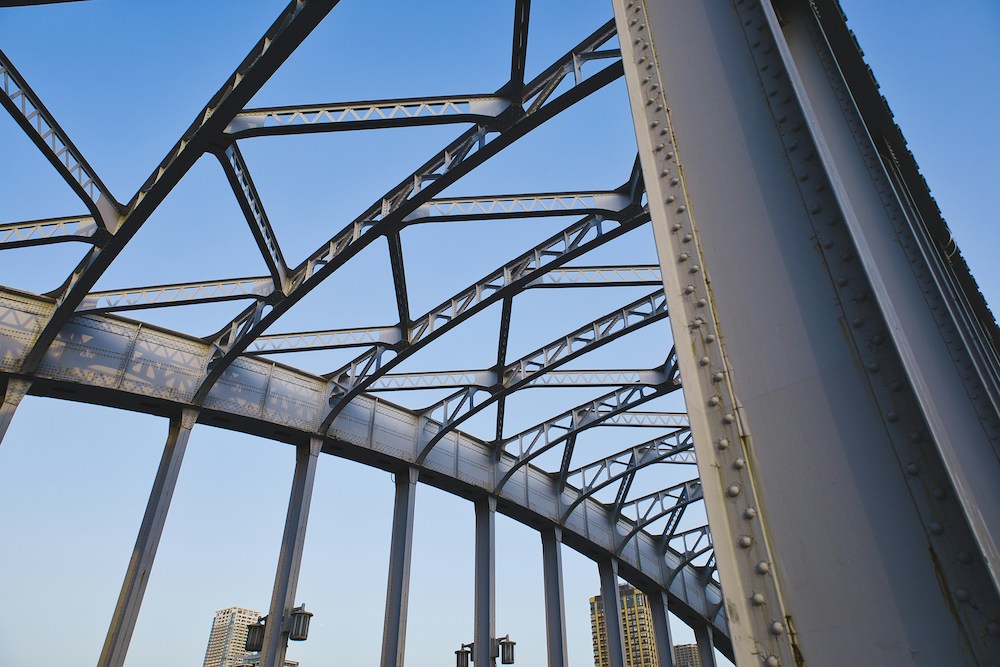
Civil Engineering
Electron beam welding is proving transformative in civil engineering, reshaping the landscape of infrastructure-related construction projects, where the integrity of welds is paramount.
Applications for Ebflow in the civil engineering sector include:
- Flat plates
- Flat plate-strips
- Long product open sections e.g., I&H universal beams
- Structural hollow sections
- Plate girders.
(Photo by Sho Shimada on Unsplash)
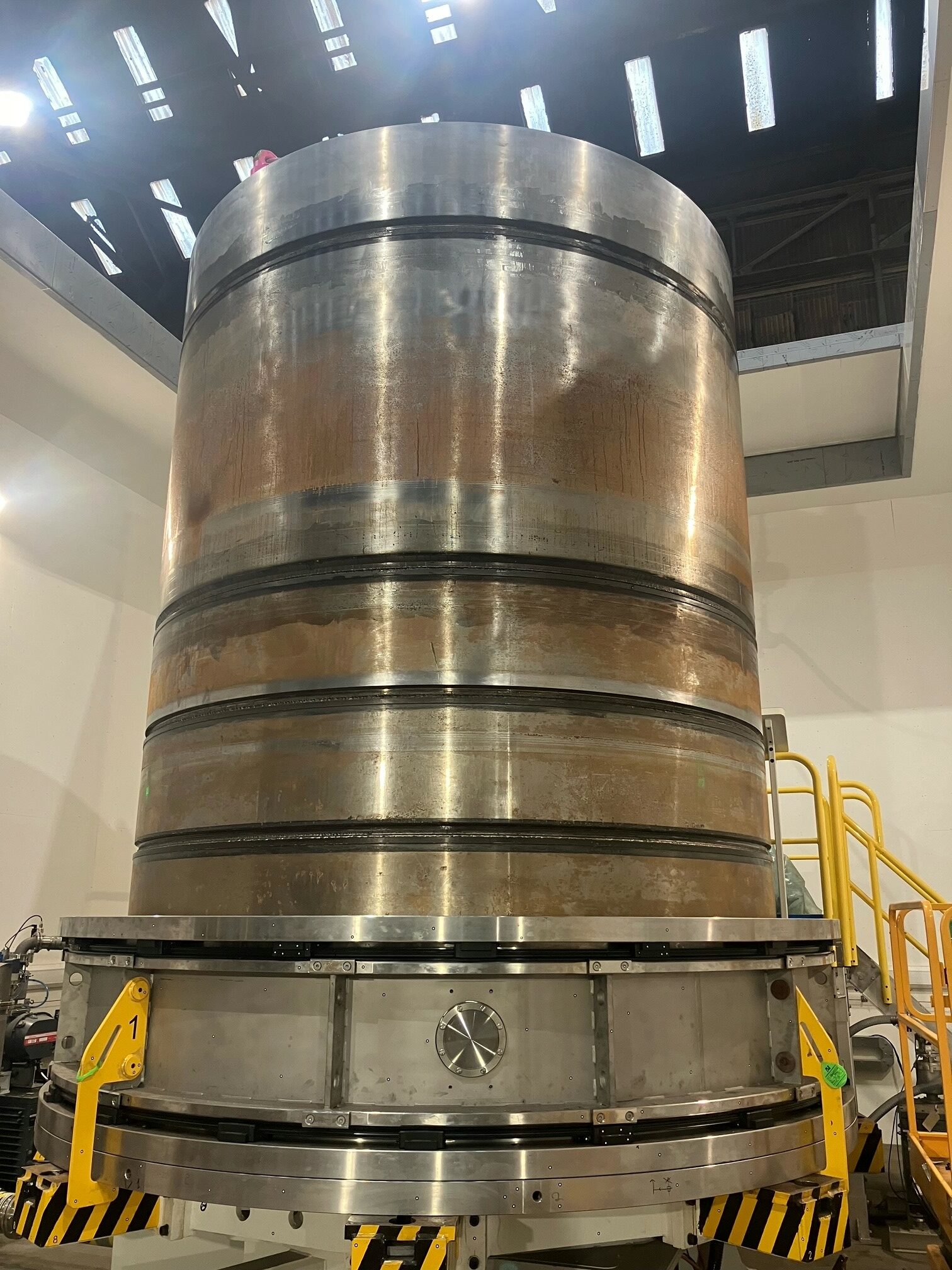
Nuclear
Ebflow is making a huge impact in the nuclear sector, drastically cutting the time needed to weld small modular reactors (SMR) and fusion reactors.
The numbers are staggering. Working with Sheffield Forgemasters, Ebflow cut the time required to weld a SMR pressure vessel demonstrator from more than a year, to less than 24 hours.
As well as reducing welding time by 99%, Ebflow also delivered the quality and precision of welds needed to ensure SMRs operate safely – setting a new standard for weld-joining thick-walled components.
Further adoption of Ebflow across the nuclear sector could reshape the future of reactor production worldwide – helping to bridge the energy gap some countries face.
Ebflow can also be used in nuclear containment applications where there is a need to store low, intermediate and high level and spent fuel for long-term geological disposal.
Read about the use of Ebflow by Sheffield Forgemasters.
What our customers say
The implication of industrialised electron beam welding technology within the nuclear industry is monumental, potentially taking high-cost welding processes out of the equation.
Dr Michael Blackmore
Senior Development Engineer & Project Lead
Sheffield Forgemasters
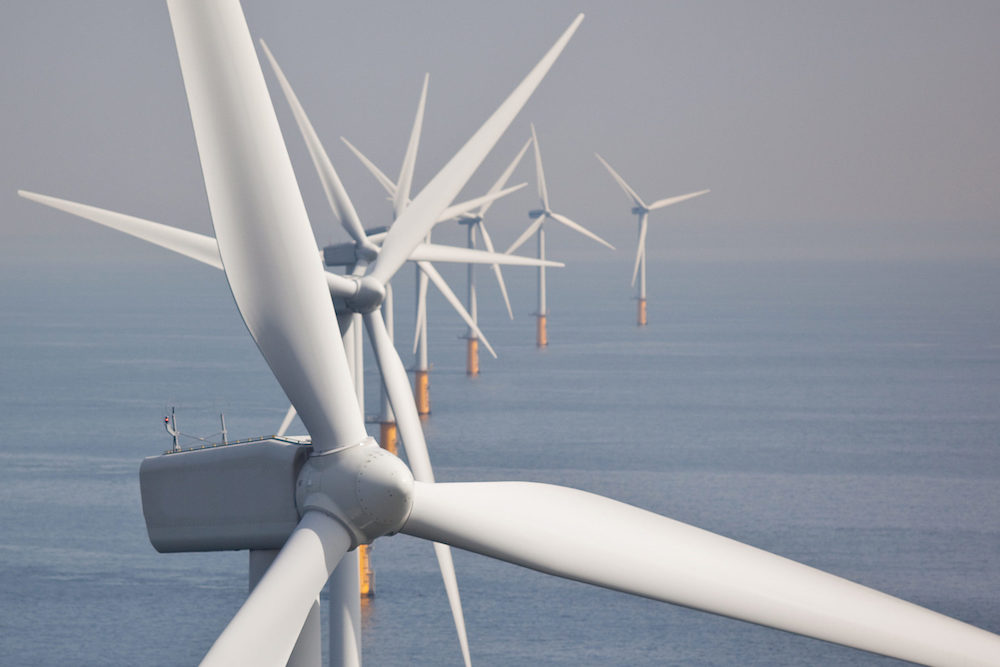
Offshore
In the offshore sector, Ebflow is award-winning and has been used to create the world’s first-ever electron beam welded section to be incorporated into a wind turbine monopile foundation.
The transition piece in question was welded significantly faster than with standard techniques. Its production was cleaner and more energy efficient. The use of Ebflow also ensured the highest quality welds, with excellent fatigue properties.
The monopile in question is now hard at work at Dogger Bank – helping to generate clean energy to power the UK’s homes and businesses.
Read more about Ebflow’s role in the RapidWeld project…
What our customers say
We’re proud to be pioneering this innovative technique on Dogger Bank Wind Farm and excited about what could be achieved by scaling up this method to pick up the pace as we work towards net zero targets.
Olly Cass
SSE Renewables Project Director for Dogger Bank Wind Farm
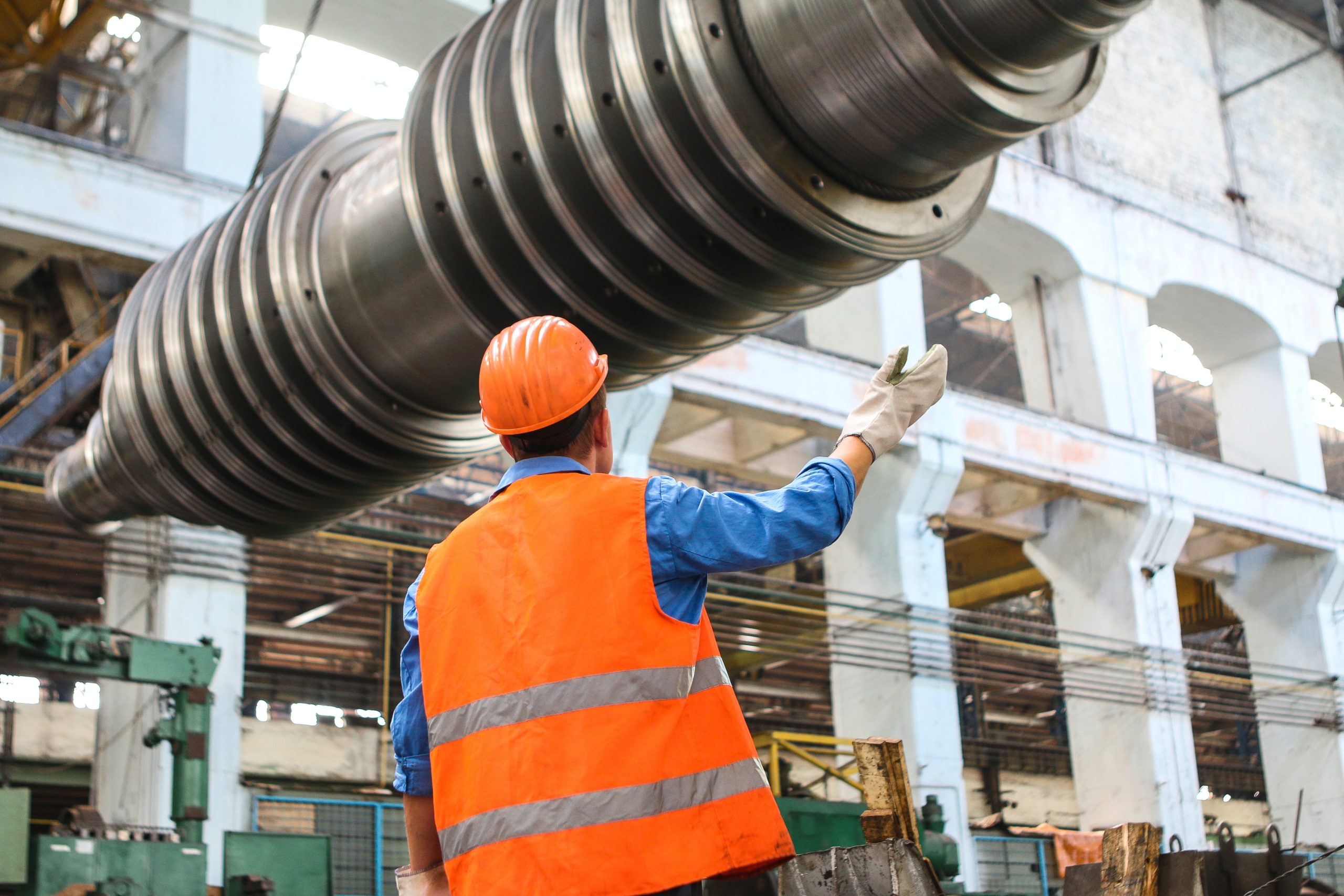
Oil & Gas
Electron beam welding is delivering game-changing results in the oil and gas sector, offering unparalleled precision and efficiency in joining critical components. Applications in the oil and gas sector include:
- Anchor piles
- Piles and followers
- J-tubes and caissons
- Riser clamps
- Flotation tanks and buoyancy tubes
- Module support frames and framing components
- Flare booms
- Subsea structures
- Heat exchangers.
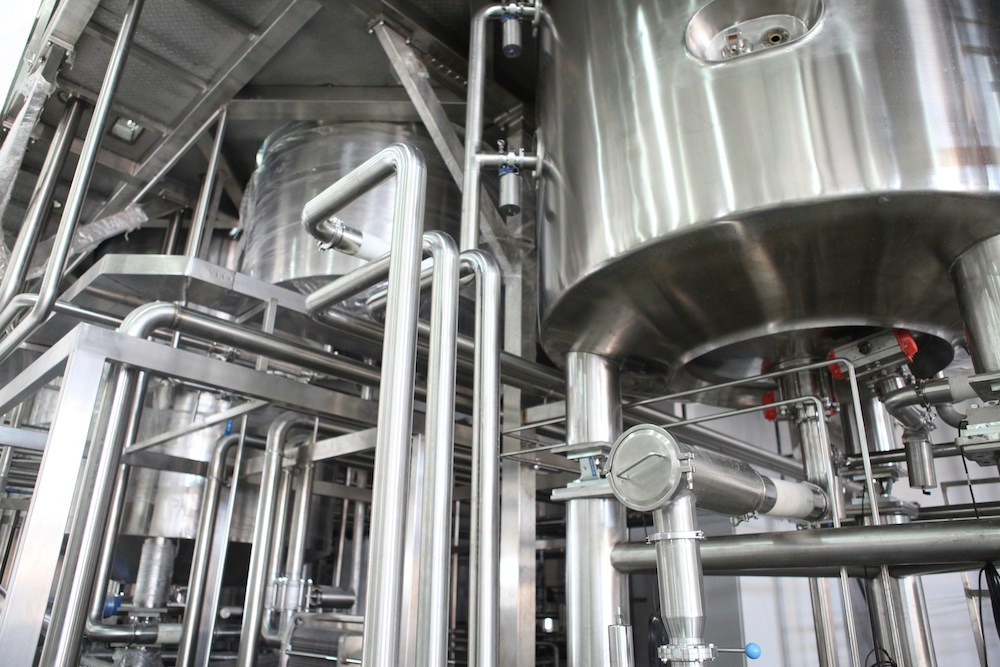
Pressure vessels
Ebflow plays a crucial role in the fabrication of pressure vessels, offering unparalleled precision and reliability in joining critical components.
Applications in the pressure vessels sector include:
- Process vessels (columns, reactors, separators, drums)
- Heat exchangers (direct cooling towers, indirect shell and tubes or plates)
- Storage tanks
- Process plants for the petrochemical / chemical and pulp and paper industries.
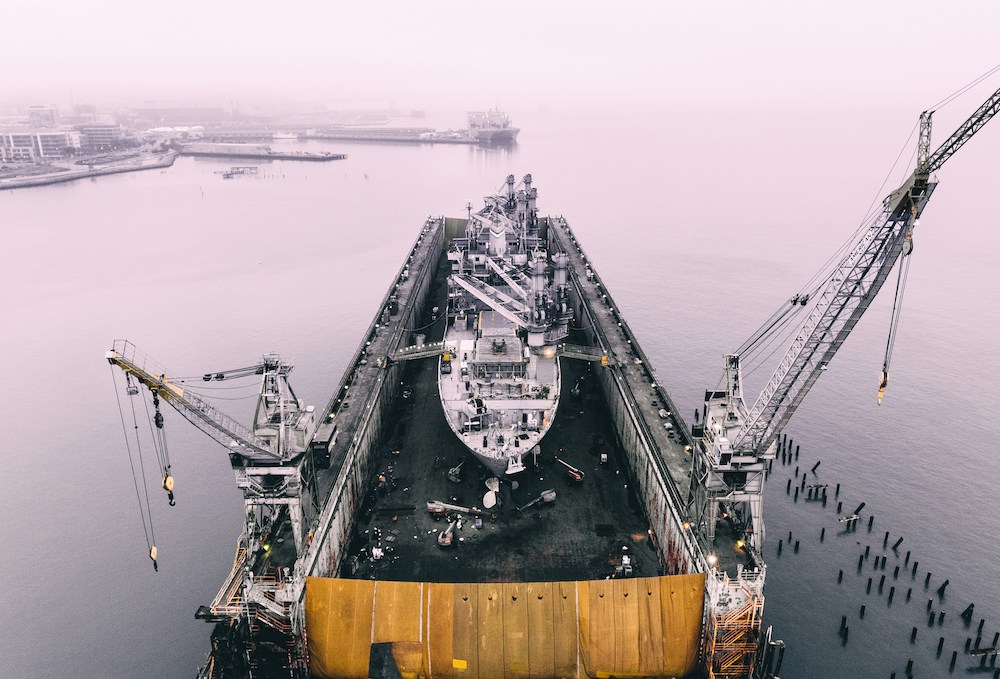
Shipbuilding
Electron beam welding is emerging as a cornerstone technology in the shipbuilding industry, revolutionising the fabrication of marine vessels.
Applications in the shipbuilding sector include:
- Modular joining
- Hull shell
- Decks
- Tanks
- Web frames
- Bulkheads
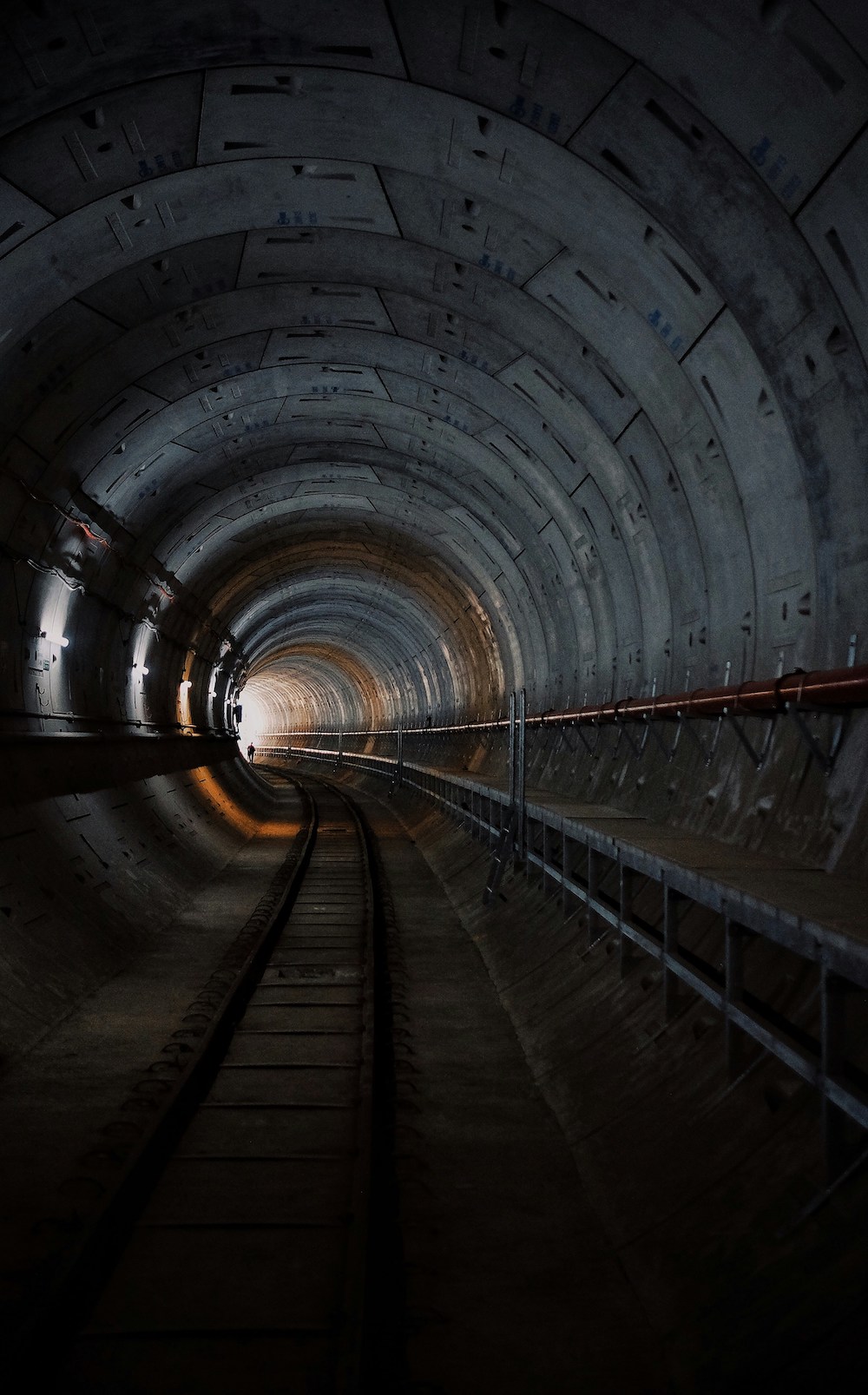
Tunnelling
Aside from the sectors mentioned here, Ebflow can be used across a range of additional applications that require thick material joining. This might typically include:
- General construction
- Earthmoving equipment
- Engineering and machinery
- Mining and quarrying
- Turbine generators
- Tunnel boring machines
If you have a welding project you’d like to discuss, please get in touch…