CASE STUDY
Sheffield Forgemasters
OVERVIEW
Client info
Sheffield Forgemasters specialises in the design and manufacture of high-integrity forgings and castings for the world’s most complex engineering challenges across defence, civil nuclear, offshore, power generation, renewables, steel plant, steel processing and ingot & bar.
Acquired by the Ministry of Defence in August 2021, Sheffield Forgemasters operates a fully integrated end-to-end manufacturing process, including steelmaking, forge, foundry, machining and testing, from a single site in Sheffield. Some of the largest bespoke engineered steel products in the world are produced by the organisation, with capacity for castings of up to 350 tonnes and forgings of up to 200 tonnes finished weight.
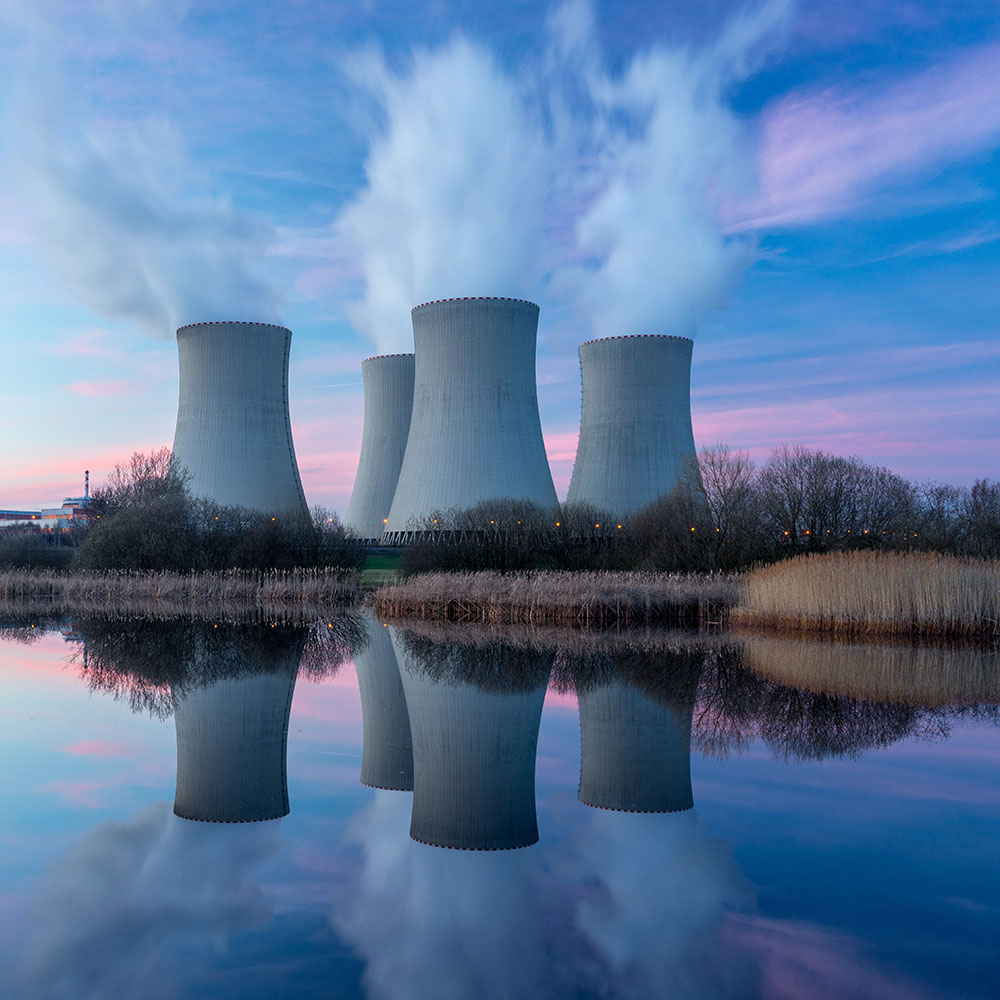
The problem
Small modular reactors (SMRs) are increasingly seen as a critical component of the nuclear industry – offering a low-carbon energy source that can offer significant advantages in terms of energy security, economic growth, safety, environmental goals and flexibility. SMRs can be constructed and deployed faster than traditional full-scale reactors. However, their development can still be lengthy with the time needed to weld a SMR pressure vessel taking up to a year – depending on requirements.
With the UK government looking to generate up to 24 gigawatts of nuclear power by 2050, Sheffield Forgemasters – the only company in the UK with the capability to manufacture the large forgings required for SMRs – was keen to find a way to speed up the development cycle.
(Photo royalty free from Shutterstock)
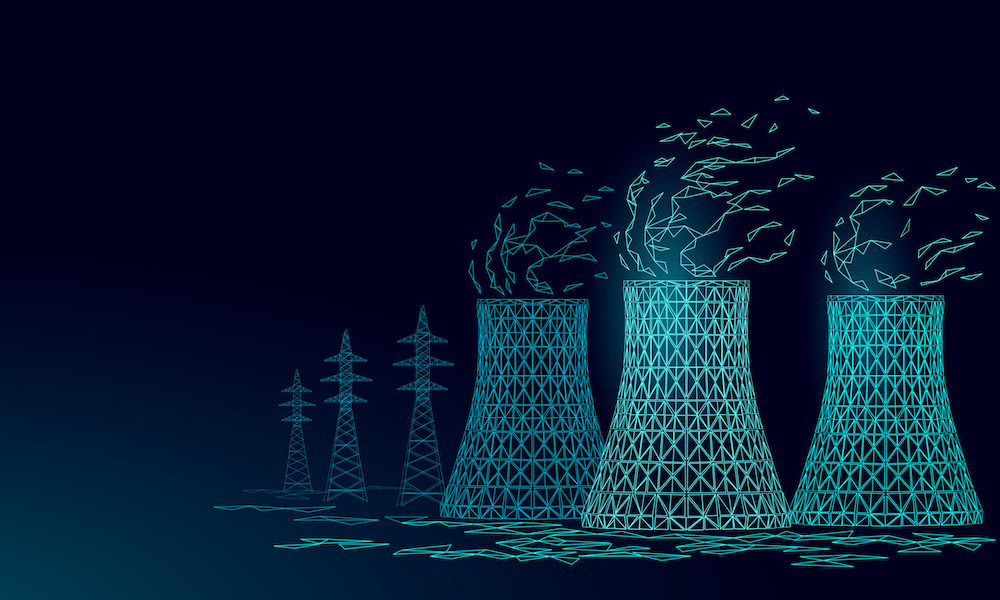
The solution
As part of a Government-funded project, Sheffield Forgemasters worked with Cambridge Vacuum Engineering to incorporate its Ebflow technology into a bespoke, large-scale electron beam welding facility at its Brightside Lane site in Yorkshire.
Ebflow is a highly advanced fusion welding process with applications across a wide range of industries. The technology utilises a focused beam of high-velocity electrons to join metal components together. The main difference to traditional welding methods is that no third-party material is introduced to make the join. This technique enables unparalleled levels of accuracy and efficiency, making it ideal for the intricate welding requirements of primary components used in mission-critical energy applications – including mini nuclear reactors.
At Sheffield Forgemasters, Ebflow’s task was to complete four thick nuclear grade welds on vessels with a diameter of three meters and a wall thickness of 200mm.
(Photo royalty free from Shutterstock)
The results
Using Ebflow, Sheffield Forgemasters was able to cut the amount of time needed to weld a SMR pressure vessel demonstrator from more than a year, to less than 24 hours.
As well as reducing welding time by an astounding 99%, Ebflow also delivered the superior quality and precision of welds needed to ensure SMRs operate safely – setting a new standard for weld-joining thick-walled components.
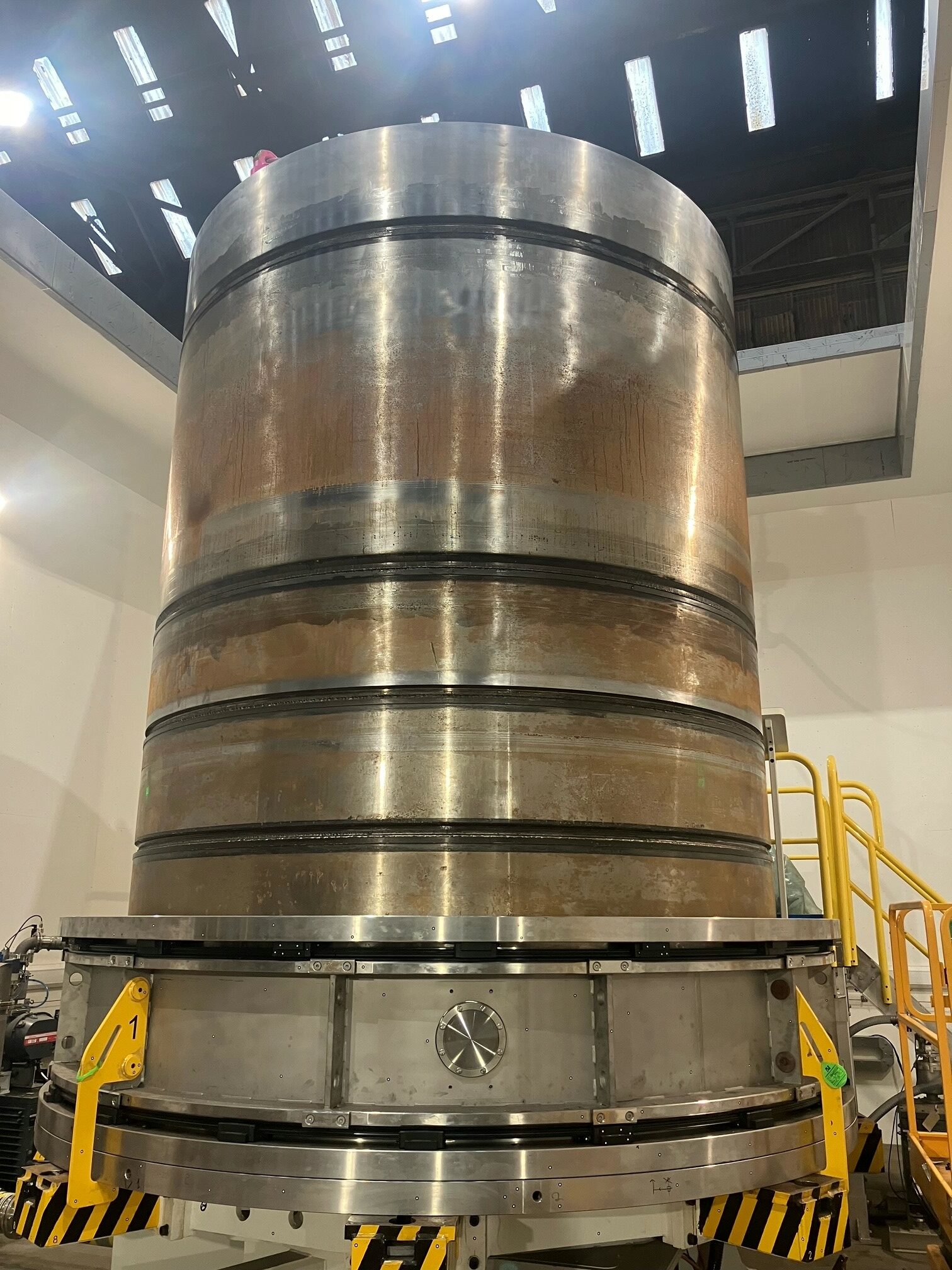
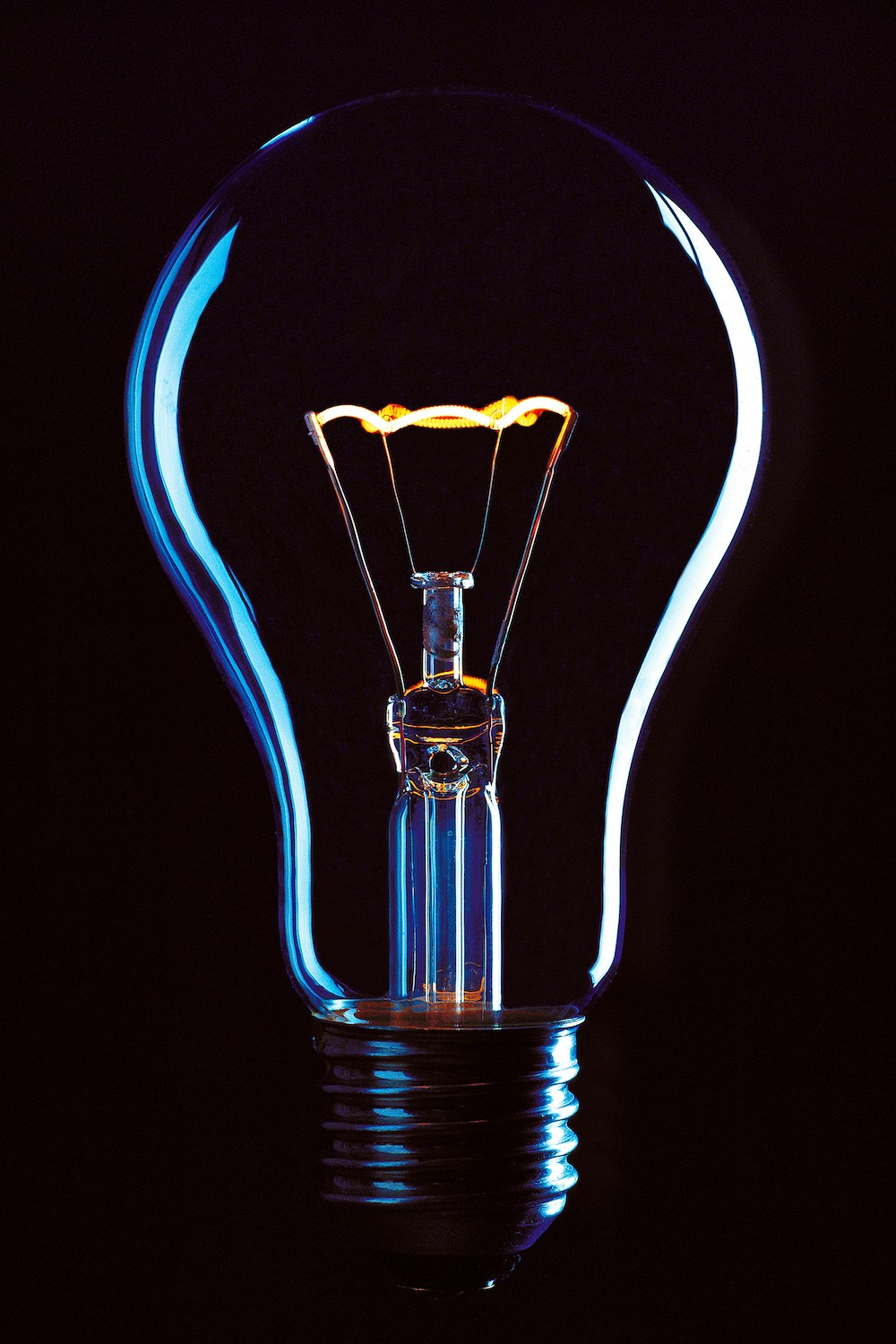
What next?
Widespread adoption of Ebflow in the nuclear sector could help reshape the future of nuclear reactor production worldwide – bridging the gap in energy markets as companies and countries look for cleaner and uninterruptable ways to generate power.
Dr Michael Blackmore, Senior Development Engineer and Project Lead at Sheffield Forgemasters, said: “The implication of industrialised Electron Beam Welding technology within the nuclear industry is monumental, potentially taking high-cost welding processes out of the equation.”
(Photo by Alessandro Bianchi on Unsplash)
What our customers say
We thank the Government’s Department for Energy Security and Net Zero for enabling the project through its Nuclear Innovation Program. We also thank our esteemed partner, Cambridge Vacuum Engineering, for their invaluable support throughout this endeavour. Their remote and on-site assistance played an instrumental role in the success of this project.
Dr Jacob Pope
Development Engineer and LEBW machine tool installation lead at Sheffield Forgemasters